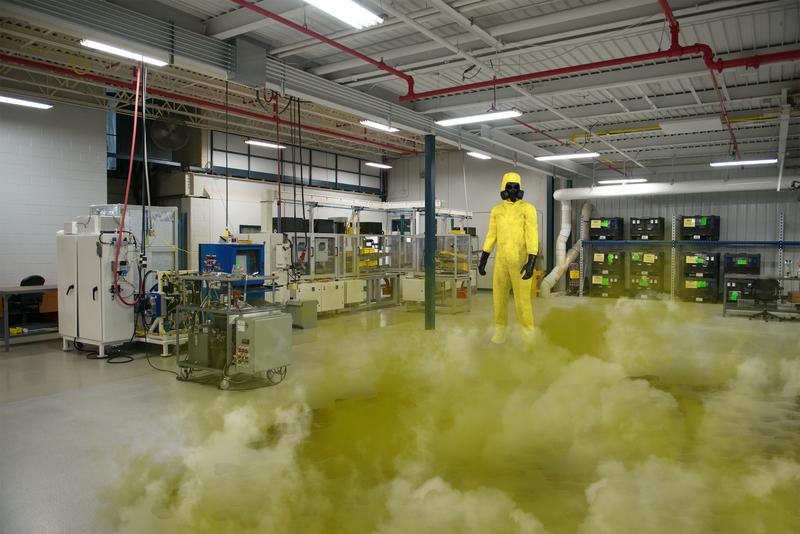
As a business, it is your responsibility to provide a safe working environment for your employees. Part of that responsibility means putting measures into place that help reduce the risk of accidents happening. This is especially important when your workplace involves the use of dangerous chemicals that can cause real harm to those handling them if done incorrectly.
Follow Basic Procedures
There are multiple basic standards and procedures that are designed specifically to reduce the risk of chemical accidents happening at work. OSHA regulations regarding different types of hazardous chemicals and basic workplace safety procedures provide such protective guidelines. These guidelines and regulations cover topics such as the proper handling and storage of hazardous chemicals. This helps prevent chemical accidents such as spills and dangerous reactions that can occur if chemicals aren't stored properly.
Read Labels
Proper labeling is another standard that helps prevent chemical accidents from occuring. These labels should include certain information about the chemical, including the hazards it poses. NFPA 704 labels can alert employees to dangerous chemicals. These labels are designed and formatted in such a way that they can be understood quickly through the use of colors, pictures, and keywords. Of course, labels don't do much good if they aren't read. Make sure your employees know how to correctly read labels so they understand them. They'll also need to know what to do with that information once they have it.
Regular Training
Regular training regarding the labeling, handling, and storage of dangerous chemicals is a key part of preventing chemical accidents from happening. It's tough to prevent a problem if you aren't given the tools to do so, which can be addressed through regular training. Rookie employees can be trained on how to read labels and how to respond to them. They should also be trained on how to handle chemical accidents in the event that they occur. New employees aren't the only ones who benefit from regular training though. It's a good idea to re-train employees on a yearly basis to make sure the information is fresh in their minds.
Accidents are an inherent risk associated with work, though measures should be taken to reduce that risk. Simple measures such as following basic procedures, reading labels, and requiring regular training for employees can help prevent chemical accidents from occurring. Putting these measures into place will help your business fulfill its obligation to provide a safe work environment for its employees.
One of the best ways to protect your employees is through getting business insurance. See what we offer here!