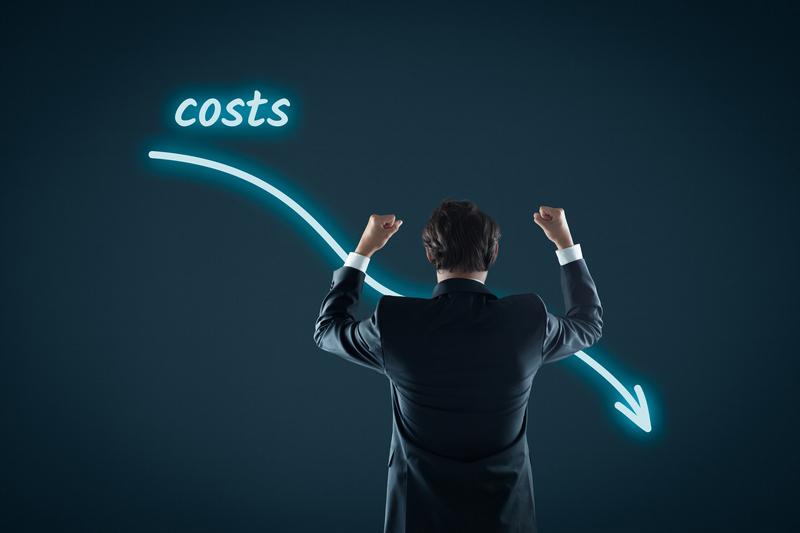
When it comes to manufacturing, profit margin is one of the best indicators of whether your products will be successful in being the foundation of a successful business. One of the easiest ways to increase profit margin is to cut production costs. Here are a few ways in which to do this.
Manufacturing Overheads
Overhead is a necessary evil within manufacturing. There are costs associated with running a business, particularly a manufacturing business, that unfortunately does not directly contribute any value to the product. Non-value added actions always exist, but they should be reduced.
Overhead is a type of waste, such as the cost of the building, wasted time, and expenses like electricity and lighting. Manufacturing overhead is necessary because there has to be a building and actual operation, but the more efficient the rest of the process, the less impact the overhead has on the bottom line.
KPIs
KPIs are frequently used as a measure of success in manufacturing, and they are used sometimes as their own form of manufacturing process style. KPI stands for Key Performance Indicators. These are measures like Units Produced, On-Time Delivery, Waste, Inventory, etc. By focusing on these measures and driving them towards the company's goals, you can reduce waste in your process and improve the efficiency of your production system.
Lean Manufacturing
Lean Manufacturing is a holistic approach that focuses on reducing waste and driving towards optimal efficiency. Lean manufacturing can reduce lead time to get products in your customer's hands more quickly. Using the 6S strategy, workers focus on reducing any inefficiency inside their own process and within the manufacturing plant as a whole. Straighten, sort, shine, standardize, set in order, and safety are the key components to this method. This has proven to be the best practice for improving the efficiency of the manufacturing process and reducing costs.
Cell-Based Manufacturing
Another production style is cell-based manufacturing. This essentially takes each portion of the process and places them in an individual cell, making them act as a unit, separated from the other areas and working together. This has obvious benefits as well as drawbacks. By focusing on working as one sole piece, the members of each cell can improve their own internal process and work out any inefficiencies and kinks without worrying about the rest of the process. There is no external source of error or inefficiency that the workers have to address, which makes process improvement easier. However, it doesn't treat the process as a whole, and there can be inefficiencies from one cell affecting another, as well as inefficiencies in transport and communication between units.
By combining Lean Manufacturing with the other options, you can truly standardize and improve the entire process. When you do that, the overhead costs will drastically drop and your process will become much smoother and more efficient overall.
Is the future of your business protected? Click here to learn more about Business Insurance and what it does for you!